
ブログ
ジャスト イン タイム生産方式の完全ガイド
投稿日:2024年6月14日
カテゴリ: 戦略
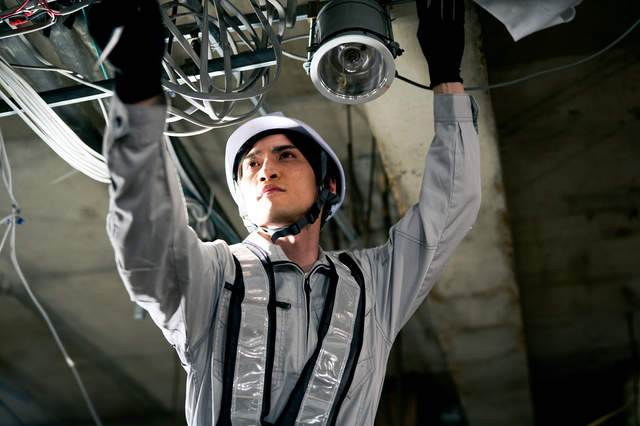
ジャスト イン タイムの概要とその重要性
ジャスト イン タイム生産方式は、生産資材や部品を必要な時に必要な量だけ調達し、在庫を最小限に抑えることで生産効率を向上させる手法です。この生産方式では、生産ラインが滞ることなく、ムダを排除し、リードタイムを短縮することが可能となります。
ジャスト イン タイムは、大量生産や在庫の抱え過ぎによるコスト増大を防ぎ、生産ライン全体の効率を高めることができます。
その結果、生産スケジュールの柔軟性や生産能力の向上、品質向上につながります。また、タイムリーな対応が求められる市場環境において、ジャスト イン タイムは競争力強化にも貢献します。
ジャスト イン タイムとは
ジャスト イン タイム(Just In Time)は、日本のトヨタ自動車が開発し、世界中で広く用いられる生産方式です。この方式では、必要な部品や資材を必要な時に必要な数量だけ生産ラインに供給します。
これにより在庫を最小限に抑え、無駄を削減し、生産効率を高めます。ジャスト イン タイムの導入には徹底した生産計画や供給ネットワークの最適化が不可欠です。
ジャスト イン タイムの歴史
アメリカの自動車産業においても、1980年代後半からジャスト イン タイムの導入が進み、その後世界中で多くの企業に取り入れられるようになりました。
ジャスト イン タイムの基本原則
ジャスト イン タイム生産方式の基本原則は、リードタイムの短縮、ムダの排除、均一生産の実現、作業者の能力活用、そして信頼性の向上です。
リードタイムの短縮には、在庫を極力抑え、必要な部品や資材が必要な時に到着できるような調達システムが重要です。在庫が減ればムダが見えてきますが、このムダを排除するためには、生産プロセス全体を見直し、無駄な作業や待ち時間をなくす工夫が必要です。
均一生産の実現は、生産ライン全体での均等な生産ペースを保つことです。これによって在庫のムラが減り、生産計画の安定性が向上します。
作業者の能力活用では、従来の作業員一人当たりのスキルを最大限に活かすような工夫が求められます。最後に、信頼性の向上には、部品供給や作業手順、生産スケジュールの確実な遂行が必要です。
これらの基本原則を実践することで、ジャスト イン タイム生産方式は生産効率化と品質向上に大きく貢献します。
後工程引き取り
後工程引き取りとは、前工程で生産された部品や製品を、次工程が必要な時に必要な量だけ引き取る仕組みです。この仕組みによって、在庫を抑えつつ、生産の流れをスムーズにし、ムダを最小限に抑えることが可能となります。
工程の流れ化
ジャスト イン タイム生産方式において重要な要素の一つが、工程の流れ化です。工程の流れ化とは、生産プロセスにおける段取りや作業の順序を最適化し、ムダをなくすことを目指す取り組みです。
工程の流れ化によって、部品や製品の移動距離を最小限に抑え、作業効率を向上させることができます。例えば、必要な部品がすぐに手の届く場所に配置されることで、作業者は無駄な移動をせずに作業に集中できます。
また、工程の流れ化によって生産ライン上での在庫が減少し、生産スペースを効率的に活用することが可能となります。これにより、スペースの有効活用や安全性の向上にも寄与します。
さらに、工程の流れ化は生産プロセス上での問題やムダを可視化しやすくする効果もあります。これにより、改善の余地や課題を明確に把握し、持続的な生産プロセスの改善につなげることができます。
工程の流れ化はジャスト イン タイム生産方式を支える重要な要素であり、生産効率や品質向上に直結する取り組みです。
必要数でタクトを決める
必要数でタクトを決める」という原則は、ジャスト イン タイム生産方式における重要な概念です。タクトとは、製品が必要とされる間隔を表し、それに基づいて生産スケジュールや作業の進捗を決定します。この原則により、在庫を最適化し、ムダを排除することが可能となります。
この原則を実践するためには、需要予測や顧客注文の変動を十分に把握し、必要な製品数を正確に見積もることが重要です。また、タクトに基づいて生産ラインの各作業工程のスケジュールを最適化し、効率的な生産を実現する必要があります。
さらに、サプライチェーン全体でタクトに合わせた調達と物流システムを構築することで、タイムリーな部品の調達や製品の出荷を実現することが可能となります。
このように、必要数でタクトを決める原則は、在庫の最適化と効率的な生産を実現するために欠かせない考え方となっています。
ジャスト イン タイムのメリット
ジャスト イン タイムのメリットには以下のようなものがあります。
1つ目は在庫削減です。ジャスト イン タイムでは必要最小限の在庫しか保有しないため、在庫コストやスペースを削減できます。
2つ目は生産効率の向上です。部品や資材が必要な時に必要なだけ供給されるため、生産ラインが滞ることが少なくなり、ムダが減少します。
3つ目は品質向上です。部品や製品が長期間在庫に残らず、新鮮な状態で使われるため、品質が保たれます。
4つ目はリードタイムの短縮です。素材や部品の調達から製品が完成するまでの時間が短縮されるため、迅速な対応が可能となります。ジャスト イン タイムを導入することで、これらのメリットを実感することができます。
在庫の最適化
ジャスト イン タイム生産方式において、在庫の最適化は重要な課題です。在庫の最適化とは、必要最小限の在庫を保ちながらも生産や販売に必要な時に必要なだけの在庫を供給できる状態を指します。ジャスト イン タイムでは、在庫がムダとされ、ムダを排除することが重要視されます。
そのため、必要な在庫レベルを把握し、正確に管理することが求められます。また、供給元との緊密な連携や情報共有が不可欠です。加えて、需要の変動などに柔軟に対応できるよう、システムやプロセスの改善を進めることも重要です。
在庫の最適化によって、在庫コストの削減やリードタイムの短縮、生産効率の向上などが実現できます。しかし、需給のバランスを取ることは容易なことではなく、慎重な計画と適切な管理が求められます。在庫の最適化を実現するためには、継続的な改善と情報共有が不可欠です。
コストの圧縮
ジャスト イン タイム生産方式によるコストの圧縮は、在庫を最小限に抑えることで保管費用やリスクを削減します。また、生産計画を柔軟に調整可能とし、予測不可能な需要変動に対応するための余剰在庫といったコストを排除します。
加えて、生産ラインのムダを削減し、生産効率を高めることで生産コストそのものも低減されます。これらの要素が組み合わさり、総合的なコスト削減効果をもたらします。
リードタイムの短縮
リードタイムの短縮についての文章を段落に分けて記載します。
1. リードタイムの短縮とは、製品やサービスを生産から顧客への提供までにかかる時間を短縮することを指します。具体的には、注文が入ってから製品が完成し、顧客に納品されるまでの時間を短縮します。
2. ジャスト イン タイム生産方式では、必要な部品や資材を必要な時に調達するため、製造中の待ち時間を減らし、生産から納品までのリードタイムを短くすることが可能です。
3. リードタイムの短縮により、顧客のニーズに素早く対応できるため、市場競争力の強化につながります。また、急な需要変動にも迅速に対応できるため、顧客満足度の向上にも寄与します。
4. さらに、リードタイムの短縮は、生産計画の柔軟性を高め、生産ライン全体の効率を向上させることができます。
ジャスト イン タイムのデメリット
ジャスト イン タイム生産方式には、効果的な一方でいくつかのデメリットも考えられます。
まず、供給遅れや不良品があった場合、生産ライン全体が混乱しやすく、大きな影響を受ける可能性があります。
また、正確な需要予測が難しい場合やサプライチェーンにおけるリスクが高い場合、適切なタイミングで部品や資材が届かないリスクが生じます。
さらに、生産ラインが停止した際に、即座に必要な部品が手に入らないというリスクもあります。
在庫切れリスク
在庫切れリスクについて、以下のような点が挙げられます。
ジャスト イン タイム生産方式では、在庫を最小限に抑えることが重視されますが、そのためには正確な需要予測やスムーズなサプライチェーンが不可欠です。しかしこれらがうまくいかない場合、仕入れ先の部品や資材の供給が途絶えることで在庫切れが発生しやすくなります。
在庫切れにより、生産ラインが停止してしまうと、それだけで大きな生産効率の低下につながります。また、急遽部品や資材を調達することでコストが増大する可能性もあります。
そのため、在庫切れリスクを軽減するためには、的確な需要予測やリスク管理、サプライチェーンの効率化が重要となります。
品質管理コスト
ジャスト イン タイム生産方式における品質管理コストは、品質管理の重要性とは裏腹に、実際には増加する傾向にあります。
この生産方式では、製品に欠陥があった場合、その製品が流れ続け、次々と欠陥品が生産されてしまう可能性があります。そのため、品質管理の重要性は非常に高く、品質管理のコストも相応にかかります。
また、製品の欠陥が生産ラインに影響を与える可能性があるため、欠陥品の排除や品質管理にますますの労力が必要となります。その結果、品質管理コストが増大することが考えられます。
さらに、供給遅れが起きた場合、急遽別のサプライヤーから部品を調達するための輸送費や急ぎ加工のためのコストもかさみます。
導入コスト
ジャスト イン タイム生産方式の導入には、さまざまなコストがかかります。まず、生産ラインの見直しや改善に伴う設備投資や自動化装置の導入など、生産プロセスを効率化するための投資が必要です。また、正確な需要の予測やスムーズな調達を行うための情報システムの導入や改修も必要となります。さらに、従業員の教育やトレーニングにもコストがかかるでしょう。
導入時の初期コストだけでなく、生産ライン全体の運用にかかるコストやリスク管理のための投資も考慮すべきです。これらのコストについてきちんと評価し、計画を立てることが重要です。
また、ジャスト イン タイムを導入することで、さまざまな面でのメリットが得られることを考慮し、長期的な視点での投資効果を見極めることも必要です。
下請け企業への負担
下請け企業への負担ジャスト イン タイム生産方式では、納入タイミングや数量が厳密に管理されるため、下請け企業にとって負担となることがあります。
まず、下請け企業は生産ラインの中核となる部品や資材を迅速かつ正確に納入する必要があります。そのため、生産計画や納入スケジュールの変更に迅速に対応する必要があります。これにより、下請け企業は生産の柔軟性を求められます。
また、ジャスト イン タイムでは在庫を最小限に抑えることが重視されます。そのため、下請け企業にとっては在庫を抱えることなく、需要に即したタイミングでの生産と納入が求められます。在庫の管理や生産ピークへの対応が、下請け企業にとっての課題となることがあります。
さらに、製品や部品の品質管理が徹底されるため、下請け企業は高品質な製品を迅速に供給する必要があります。これにより、品質管理システムの整備や品質向上活動に取り組む必要があります。
そのため、下請け企業がジャスト イン タイムに対応するためには、生産能力や品質管理システムの強化が求められます。
大量調達の難しさ
大量調達の難しさについて、以下のように説明できます。
1.在庫コストの増大
大量調達は、一度に大量の部品や資材を調達することを意味します。そのため、調達コストや保管コストが増大し、資金が縛られることにつながります。
2.需給バランスの難しさ
大量調達を行う場合、需要の予測精度が非常に高くなければなりません。需要予測の誤差が生じた場合、在庫の増加や減少が生じ、効率的な生産が阻害される可能性があります。
3.過剰在庫の危険性
大量調達を行った際、需要が予測よりも低い場合、過剰在庫が発生しやすくなります。この過剰在庫はコストの無駄遣いとなります。
環境負荷の増加
ジャスト イン タイム生産方式には環境負荷の増加という課題もあります。
かんばん方式とジャスト イン タイム
ジャスト イン タイム(JIT)とかんばん方式は、生産管理の手法として密接に関連しています。かんばん方式は、在庫の制御と生産のペースを調整するための仕組みであり、ジャスト イン タイムの実践に欠かせません。
かんばんとは、部品や製品を適切なタイミングで必要な数量だけ生産・供給するための情報を表したツールです。かんばんは、生産ライン上での在庫の増減や引取時の生産情報を視覚的に管理し、生産のムダを最小限に抑えます。
ジャスト イン タイムでは、かんばんを活用して生産現場を適切に制御し、在庫を抑えながら生産を行います。かんばんを用いることで、部品や製品の不足や過剰在庫といった問題を効果的に防ぐことが可能となります。
このように、かんばん方式とジャスト イン タイムは、生産効率化やムダの削減、正確な生産スケジュールの策定において連携し合うことで、生産現場の効率化を図ります。
かんばん方式の概念
かんばん方式は、日本の自動車産業で生まれた生産管理手法であり、生産の流れを視覚的に管理するための仕組みです。
この方式では、かんばんと呼ばれるタグやカードに情報を記載し、それを用いて部品や製品の生産・供給を制御します。
具体的には、製品が次の工程に必要になる時に、かんばんを引き取り、その情報に基づいて必要な数だけ部品や製品を生産・供給します。
また、かんばんを使用することで、在庫の増減や生産ペースの調整が視覚的に把握しやすくなり、生産のムダを減らすことができます。
このように、かんばん方式は、生産現場における在庫管理や生産スケジュールの最適化に貢献し、ジャスト イン タイム生産方式の実践において重要な役割を果たしています。
かんばん方式のメリット
かんばん方式のメリット
トヨタ生産方式とジャスト イン タイム
トヨタ生産方式は、ジャスト イン タイム(JIT)を基盤とした生産システムで、1950年代にトヨタ自動車で開発されました。この方式は、在庫をなるべく抑え、生産現場でのムダを徹底的に排除することを特徴としています。
トヨタ生産方式は、生産ライン全体が滞ることなく効率よく稼働するように設計されており、品質の向上や生産効率の最大化を実現しています。この方式では、従来の大量生産方式とは異なり、部品や製品が必要に応じて適切なタイミングで供給されるため、在庫の過剰や品質の低下を防ぐことができます。
また、トヨタ生産方式は社員全体が参加し、改善提案を積極的に行うことで生産現場を改善し続ける仕組みを構築しており、その結果、効率化や品質向上が推進されています。トヨタ生産方式は、生産現場の革新的な変革をもたらし、世界中の企業に多大な影響を与えています。
トヨタ生産方式の概要
トヨタ生産方式は、トヨタ自動車が開発した生産システムであり、世界中の企業に多大な影響を与えています。この方式は、1950年代にトヨタ自動車が取り組んだ経営の改善活動の一環として生まれました。
トヨタ生産方式では、無駄を最小限に抑えるための様々な取り組みが行われています。在庫を抑え、生産ライン全体が滞ることなく効率的に稼働するように設計されています。部品や製品は必要な時に必要なだけ供給されるため、在庫過剰やムダが排除されます。
さらに、トヨタ生産方式では、社員全体が参加し、改善提案を行うことが奨励されています。このような取り組みにより、生産現場での改善が継続的に行われ、効率化や品質向上が実現されています。
トヨタ生産方式は、その特徴的な取り組みにより、世界中の企業に革新的な変革をもたらし、生産効率化や品質向上のための貴重な教訓を提供しています。
トヨタ生産方式のメリット
トヨタ生産方式のメリットは、さまざまな側面から生産効率化や品質向上に大きな影響を与えています。第一に、トヨタ生産方式は在庫を極力抑えることで、資産の効率的な活用とコストの削減が可能となります。在庫が減ることで、倉庫スペースを最小限に抑え、運転資金や保管コストの削減につながります。
このように在庫の抱えるコストリスクを軽減することができるのです。さらに、在庫が少ない分、不良品や廃棄物を発生させるリスクも低減し、製品の品質向上に直結します。品質を確保するための細心の注意や検査体制の確立により、顧客満足度の向上にも寄与します。
また、トヨタ生産方式では生産プロセスの改善を積極的に行うため、労働力の有効活用や生産工程の改革が促進されます。
さらに、トヨタ生産方式は従業員を尊重し、積極的な参加とアイデアの提案を奨励するため、働きやすい環境を構築し、労働者のモチベーション向上にもつながっています。
これらのメリットが組み合わさり、トヨタ生産方式は生産効率化や品質向上において大きな利益をもたらしています。
事例紹介:ジャスト イン タイム導入成功例
ジャスト イン タイム生産方式の導入に成功した企業事例を紹介します。日産自動車では、部品の調達を細かい単位で行い、生産ラインとのタイムリーな連携を図ることで在庫を大幅に削減しました。
これにより、生産効率の向上、不良品の減少、スペースの有効活用など様々な効果を得ることができました。また、トヨタ自動車もジャスト イン タイムを導入し、納期の短縮や製品のバリエーション増加など多方面にわたって効果を上げています。
企業Aの成功事例
企業Aの成功事例について、以下にご紹介いたします。
企業Aはジャスト イン タイムを導入することで、効率的な生産体制を構築しました。まず、部品の調達から生産ラインへの供給までのプロセスを見直し、ムダを徹底的に排除しました。これにより、在庫の過剰や不良品の発生を抑えることができました。
さらに、企業Aはサプライヤーとの緊密な連携を強化し、生産に必要な部品や資材をタイムリーに調達する体制を整えました。これにより、生産ラインのストップを最小限に抑えることができ、生産効率の向上につながりました。
また、ジャスト イン タイムの原則に基づいた生産計画を策定し、短期的な需要変動にも迅速に対応できる柔軟性を手に入れました。このことが、市場動向の変化に対応し、競争力を維持するための重要な要素となりました。
企業Bの成功事例
企業Bの成功事例をご紹介します。
企業Bはジャスト イン タイムを導入することで、大きな成果を上げました。まず、生産ラインがスムーズに稼働し、余剰在庫の負担無く、製品を需要に応じて的確に生産することが可能となりました。これにより、生産効率が向上し、非生産時間が減少しました。
さらに、ジャスト イン タイムの導入により、不良品や在庫ロスが減り、製品の品質向上につながりました。また、生産設備の有効活用が図れるようになり、設備の設置スペースの最適化が実現しました。
さらに、納期の短縮や顧客の需要変化に柔軟に対応できるようになり、市場競争力の強化にもつながりました。企業Bはジャスト イン タイム導入により、生産効率化、コスト削減、品質向上など多方面での効果を実感し、競争環境において一層の成長を遂げることができました。
ジャスト イン タイムのデジタル化
ジャスト イン タイムのデジタル化は、現代の生産管理において重要なテーマとなっています。デジタル技術の進化により、生産ライン全体をリアルタイムでモニタリングし、生産計画や在庫管理を効率的に行うことが可能となりました。
デジタル化による生産ラインのモニタリングでは、センサー技術やIoT(Internet of Things)デバイスを活用して、各工程や機器の稼働状況や生産速度、品質データなどをリアルタイムで収集し、可視化することができます。これにより、生産ライン全体の稼働状況を把握しやすくし、トラブルや効率化の余地を素早く把握することができます。
また、デジタル化による在庫管理では、需要予測に基づいた適切な在庫レベルの維持や、調達のタイミングを最適化することが可能となります。
さらに、クラウドベースの生産管理システムによって、複数工場間の情報共有やリアルタイムの生産スケジュール調整が容易になり、生産全体の効率化が図れます。
ジャスト イン タイムのデジタル化は、生産効率の向上や生産計画の最適化、在庫の最適化など多岐にわたるメリットをもたらします。
スマートマットクラウドの導入
スマートマットクラウドの導入は、ジャスト イン タイム生産方式をより効果的に実現するための重要な一歩です。このクラウドベースのシステムは、複数工場間での生産情報のリアルタイム共有や生産スケジュールの最適化を可能にします。
さらに、スマートマットクラウドは、需要予測に基づいた在庫の最適化や調達の効率化もサポートします。
また、スマートマットクラウドを活用することで、生産ラインの各工程や機器の稼働状況や品質データなどをリアルタイムでモニタリングし、生産効率の向上やトラブルの早期発見につなげることができます。さらに、クラウド上でのデータ解析により、生産プロセスの改善や効率化の余地の発見が可能となります。
スマートマットクラウドの導入によって、生産管理全体の効率化と品質向上を実現できるだけでなく、競争力強化にもつながることが期待されます。このように、デジタル技術の活用とジャスト イン タイム生産方式の組み合わせは、現代の生産管理において重要な戦略と言えるでしょう。
まとめ
ジャスト イン タイム生産方式は、生産ラインをスムーズに保つとともに、品質向上やコスト削減にもつながります。ジャスト イン タイムによって、部品や材料の不必要な在庫が減少し、ロスを最小限に抑えることが可能となります。
さらに、製品の生産が顧客の需要に合わせて行われるため、市場の需要変化に迅速に対応することができます。この生産方式は、労力や時間を無駄にしない効率的な生産プロセスを築き上げることで、競争力のあるビジネス運営を実現します。
また、サプライチェーン全体を通じて、信頼性の高い取引関係を構築することもでき、企業間の連携を強化します。ジャスト イン タイムの導入により、迅速かつ効率的な生産を実現し、競争優位性を獲得できます。